What You Will Learn
With this thorough guide, find out how best to control welding fume smoke on your shop floor. To guarantee a safe and healthy working environment, we address the best gadgets and systems—fume extractors, downdraft tables, and ventilation solutions. Investigate useful advice and tools designed for industrial environments to lower fume exposure and enhance the air quality for your employees.
Table of Contents
Portable Fume Extractors
Stationary Fume Extractors
On-Torch Fume Extractors
Flexible Extraction Arms
Articulating Extraction Arms
Downdraft Weld Tables
Welding Booths with Ventilation Systems
Welding Curtains with Ventilation Systems
Respiratory Protective Equipment (RPE)
Floor Mounted Welding Hoods - Strips
Hanging Welding Hoods Strips
Hanging Welding Hoods - Large
Welding Fume Enclosures - Large Area - Style 1
Welding Fume Enclosures - Large Area - Style 2
Welding Fume Enclosures - Small Area - Style 1
Welding Fume Enclosures - Small Area - Style 2
Welding Fume Enclosures - Small Area - Style 3
Common Questions
Summary
Welding Fume Extractors:
Portable Fume Extractors
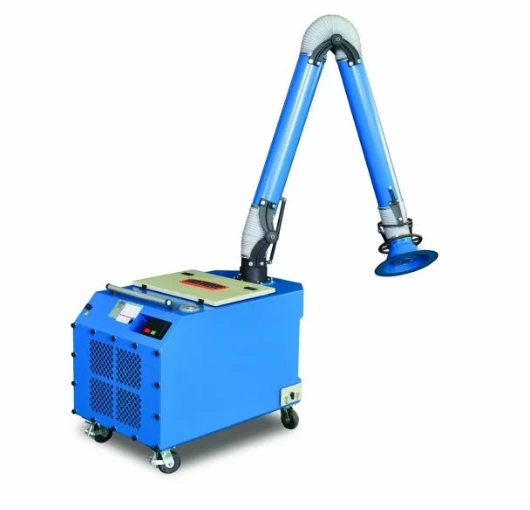
Essential tools used in many different industrial environments to capture and filter created toxic vapors and particulates from operations including welding, soldering, and chemical applications are portable fume extractors. Designed for mobility, these devices can be quickly relocated to various workstations, offering a flexible approach for fume extraction in cases when permanent installations would not be practical.
Usually comprising a strong fan drawing in contaminated air via a filtering system—which usually includes HEPA and activated carbon filters—these extractors While the carbon filter adsorbs dangerous gasses and smells, the HEPA filter gathers fine particulate matter, therefore guaranteeing that the air expelled back into the environment is clean and safe to breathe.
Portable fume extractors have one main benefit: they may be positioned near the source of fumes, therefore greatly enhancing their efficiency in gathering pollutants before they can spread into the surrounding air. This close closeness increases workplace safety by lowering workers' total exposure to dangerous fumes. Furthermore, the portability of these devices makes it possible for them to be used in several uses throughout different parts of a facility, therefore providing a flexible and affordable way to keep air quality in surroundings where hazardous gasses are produced.
The Pros and Cons
Pros of Portable Fume Extractors for Welding Fume Control:
- Mobility and Flexibility: Easily transported to several welding sites, portable fume extractors offer targeted fume management anywhere required. This is especially helpful in big buildings or locations lacking fixed welding assignments.
- Effective Fume Capture: Portable fume extractors effectively collect fumes at the source when placed near the welding point, therefore lowering the airborne pollution in the workplace.
- Cost-Effective: Portable systems are sometimes more reasonably priced than a permanent fume extraction system, which helps smaller businesses or temporary setups save money.
- Versatility: In a workshop or industrial facility, these extractors are a flexible tool since they may be used for several welding operations and other activities creating dangerous vapors.
- Easy Maintenance: Usually built for low maintenance, portable fume extractors feature easily replaceable filters that can be cleaned or replaced as needed, therefore guaranteeing continuous operation with minimum downtime.
Cons of Portable Fume Extractors for Welding Fume Control:
- Limited Coverage Area: Portable fume extractors are made to cover certain workstations, so they could not be enough for bigger areas or several welding stations without constant mobility.
- Dependence on Proper Positioning: The proximity of a portable fume extractor to the welding source determines its efficiency mostly. Its efficiency may be lowered by improper placement, which increases the air pollution.
- Noise Levels: Certain portable fume extractors can be loud when running, which might be unpleasant for employees or disturbing in a crowded workplace.
- Frequent Filter Replacement: Filters in portable fume extractors may need to be updated or cleaned often depending on their degree of use. Potential downtime and continuing maintenance expenses follow from this.
- Power Requirements: Portable fume extractors need a power source, which could restrict their location in some places or call for extra extension cords or power outlets, thereby perhaps resulting in a messy workplace.
Stationary Fume Extractors
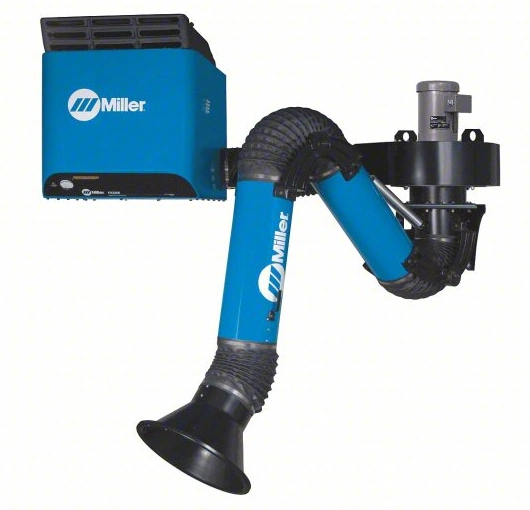
For the purpose of eliminating dangerous gases, smoke, and particulates from the air in manufacturing, industrial, and laboratory settings, stationary fume extractors are indispensable equipment. Because these machines are stationary and usually attached to filtration or ventilation systems, they are perfect for workstations where dangerous vapors are frequently generated, such soldering, welding, and chemical processing facilities.
Stationary fume extractors effectively remove pollutants from the air at their source by using powerful fans and filters (such activated carbon or HEPA) to create a safer and cleaner working environment. Some variants can manage several kinds of airborne contaminants, from dust and particles to poisonous gasses, because they have multi-stage filtration.
Usually, these extractors are built into workbenches or installed on walls or ceilings. Their purpose is to offer consistent, targeted extraction, mitigating exposure to detrimental agents and safeguarding the well-being of laborers and their tools. For added convenience, advanced models may also have features like automatic filter cleaning systems or movable extraction arms.
Because of their stationary design, they are extremely dependable for extended usage in fixed workspaces, guaranteeing adherence to air quality standards and reducing hazards to the environment and public health in industrial environments.
The Pros and Cons
Pros of Stationary Fume Extractors:
- Effective Contaminant Removal: Cleaner air is ensured by their efficient removal of smoke, toxic odors, and particulates by consistent and strong filtration.
- Continuous Operation: These units ensure extraction around-the-clock because of their stationary design, which makes them perfect for continuous usage in permanent places like welding or soldering stations.
- Space-saving Design: In crowded work areas, stationary extractors can be integrated into workbenches or installed on walls or ceilings to free up valuable floor space.
- High Filtration Efficiency: Numerous versions come with multi-stage filters that can handle a variety of pollutants, like activated carbon or HEPA filters.
- Durability and Reliability: Static extractors are a dependable investment because they are made for prolonged usage and are typically more sturdy and long-lasting than portable models.
Cons of Stationary Fume Extractors:
- Limited Mobility: Static extractors, as the name implies, are set in place, which makes them inappropriate for activities requiring flexibility or mobility in various locations.
- Higher Installation Costs: The initial price of installing a fixed system may increase if professional setup, including ductwork and mounting, is needed.
- Potential Noise Levels: Stationary units can make a lot of noise, depending on the model and power, therefore extra soundproofing may be needed.
- Maintenance Needs: The system must have regular maintenance to function properly, such as filter replacements and system cleaning, which raises the cost of continuous operations.
- Limited Coverage Area: Since these units are intended for particular zones, larger workspaces can require the use of more extractors.
On-Torch Fume Extractors
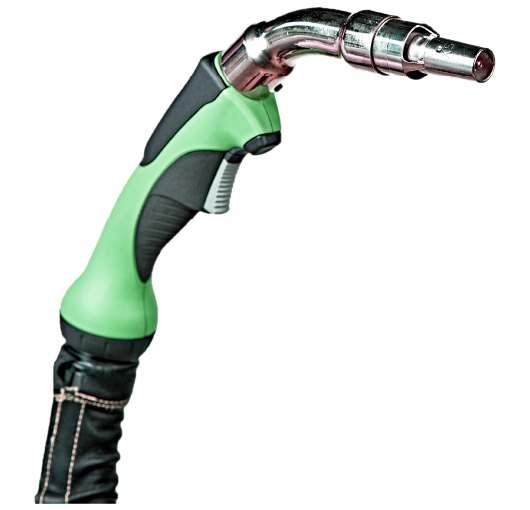
During welding operations, on-torch fume extractors are specialized equipment used to extract toxic vapors right from the source. These extractors, which are built into the welding torch itself, enable the quick removal of fumes as they are generated, in contrast to stationary or portable equipment. By doing this, it is made sure that harmful gasses, smoke, and particulates are removed before they have a chance to enter the nearby workspace.
On-torch fume extractors usually consist of a little extraction system or nozzle that is fastened to the welding torch. Flexible hoses connect the system to an external extraction unit, where hazardous material-removing filters receive the contaminated air. These extractors are especially useful in situations when conventional fume extraction systems might not be feasible or effective enough, including when welding in tight or difficult-to-reach areas.
The main benefit of on-torch fume extractors is its ability to effectively remove fumes from the source, giving welders the best possible protection. They also reduce the requirement for bulky overhead extraction systems, which gives them flexibility and a small footprint. The additional extraction system, however, may have an impact on the welding torch's weight and balance. As a result, these units must be adjusted carefully to prevent welding interruptions.
The Pros and Cons
Pros of On-Torch Fume Extractors:
- Fume Extraction at the Source: By directly capturing toxic vapors from the welding flame, these systems guarantee quick and efficient elimination of impurities before they have a chance to spread.
- Increased Safety for Welders: Welders' health and safety are improved with on-torch extractors, which limit their exposure to dangerous gases and smoke.
- Space-Saving: On-torch extractors are perfect for smaller or cramped work spaces because they don't require overhead ductwork or a vast amount of room, unlike large stationary systems.
- Flexibility for Confined Spaces: These extractors are especially helpful in welding locations that are confined or difficult to access, where conventional extraction techniques would not be practical.
- Portable and Adaptable: These systems travel with the welder since they are integrated with the welding torch, enabling extraction wherever welding is being done.
Cons of On-Torch Fume Extractors:
- Added Weight and Bulk: The welding torch's weight and mass may rise due to the additional equipment attached to it, which could be uncomfortable or limit its agility.
- Potential for Disrupting the Welding Process: The extractor might impact the quality of the weld if it is not adjusted correctly, interfering with the welding arc or airflow.
- Limited Extraction Power:It's possible that fixed machines offer more powerful extraction than torch systems, particularly in situations with high fume volumes or during heavy-duty welding.
- Maintenance and Wear: Because of its continuous movement, the integrated system could be more prone to wear and tear, necessitating regular maintenance or part replacement.
- Higher Initial Costs: When compared to more affordable fixed or portable fume extractors, torch fume extractors are typically more costly up front.
Fume Extraction Arms:
Flexible Extraction Arms
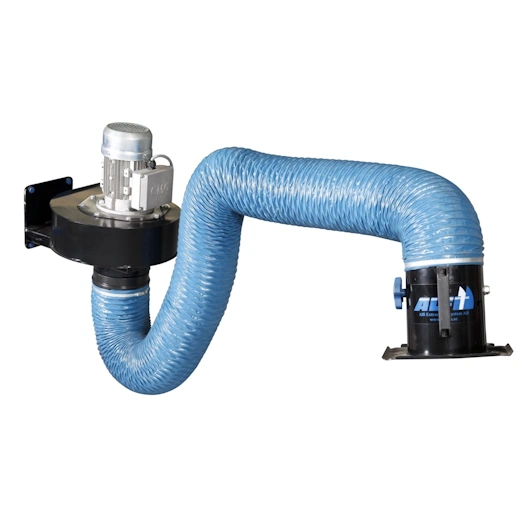
Versatile fume extraction tools called flexible extraction arms are made to extract smoke, dust, and other hazardous airborne particles straight from the site of production. Usually, these arms are utilized in labs, workshops, and industrial settings where potentially dangerous materials are released during processes like grinding, welding, soldering, and chemical reactions.
The capacity of flexible extraction arms to bend and adjust to different orientations allows for exact positioning close to the source of the emission. This is what makes them unique. They may be extended, turned, and positioned as needed. They are frequently installed on walls, ceilings, or workbenches. Clean air is released back into the workspace after the contaminated air is filtered by the extraction arm, which is attached to a central ventilation or filtration system.
The arms are usually fitted with hoods or nozzles that efficiently trap pollutants, and they are available in a variety of diameters and lengths to accommodate a range of applications. Because of their versatility, which allows the arm to be readily moved to cover various workstation areas, they are incredibly useful for employees.
Flexible extraction arms are highly valued for enhancing workplace safety and air quality by lowering exposure to dangerous airborne particles. To guarantee the best possible airflow and efficiency, they might need to have frequent maintenance done.
The Pros and Cons
Pros of Flexible Extraction Arms:
- Precise Positioning: Because of the arm's flexibility, users can aim it straight at the source of fumes or particulates to ensure effective extraction.
- Versatility: They are suited to a variety of sectors because to their wide range of uses, which include grinding, chemical processing, soldering, and welding.
- Space-Saving: Flexible extraction arms are usually installed on workbenches, walls, or ceilings to conserve floor space and allow for easy adjustment without requiring extra space.
- Improved Air Quality: They greatly enhance the safety and quality of the air for those working in dangerous areas by absorbing dangerous gases and particles at their source.
- Ease of Use: Because they are lightweight and flexible, workers may easily move their arms and modify their positions as needed while performing tasks.
Cons of Flexible Extraction Arms:
- Limited Coverage Area: Greater workspaces may need additional arms or extraction devices because they are only effective within a certain radius around the arm.
- Ongoing Maintenance: In order to prevent obstructions and guarantee enough airflow, routine cleaning and maintenance are required, which may raise operating expenses.
- Potential Obstruction: Depending on how it's set up, the arm can block the workspace or get in the way of the user's movements.
- Initial Installation Cost: Installation may be expensive and necessitate expert setup, depending on the mounting mechanism and the extraction unit it links to.
- Lower Power for Heavy-Duty Tasks:Flexible extraction arms might not have the same suction power as bigger, fixed devices in extremely demanding applications, such as large-scale operations or heavy-duty welding.
Articulating Extraction Arms
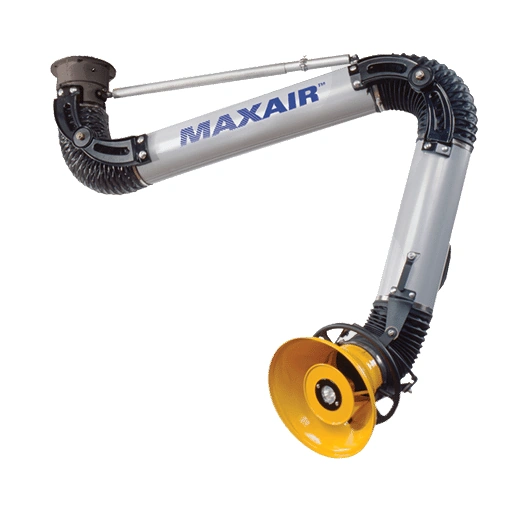
Innovative ventilation solutions called articulating extraction arms are made expressly to collect smoke, dust, and odors from the air in a variety of industrial and workshop environments. These arms can reach great distances and be positioned precisely because of their numerous joints and flexible segments. Users may easily aim the extraction hood directly toward the source of emissions, whether from welding, soldering, grinding, or other procedures that produce hazardous particles, thanks to this design's adjustable arm's length and angle.
Articulating extraction arms, which are usually installed on walls, ceilings, or benches, include a hood or nozzle at the end that efficiently collects pollutants as they are emitted. A central extraction system, to which the arms are connected, filters the tainted air and maintains a higher standard of air quality in the workspace. Because to their articulating nature, they may reach confined or problematic locations that would be difficult for conventional extraction devices to access.
The advantages of articulating extraction arms include increased flexibility in use, better air quality, and increased worker safety. To guarantee effective airflow and to avoid clogs, they need to be maintained on a regular basis, which will guarantee their continued effectiveness over time. All things considered, they represent a wise investment for settings where air quality is a major concern.
The Pros and Cons
Downdraft Tables:
Downdraft Weld Tables
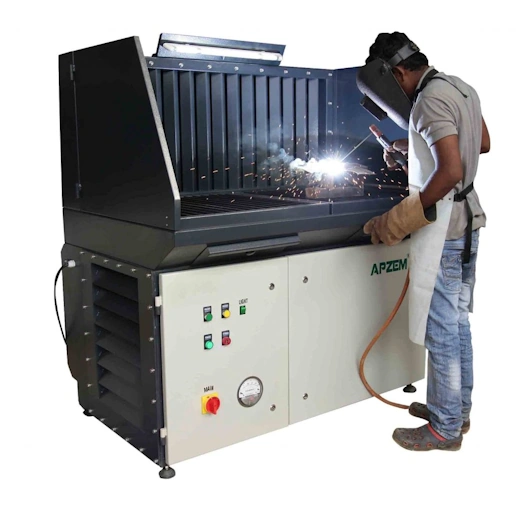
Specialized workstations called downdraft weld tables are made to improve weld operations' productivity and safety. These tables have a built-in fume extraction system that pulls smoke, welding fumes, and other airborne particles through the work surface and downward. By efficiently removing dangerous impurities at their source, this design enhances air quality and gives welders a healthier workplace.
Downdraft weld tables are often made of sturdy materials like steel and have perforated surfaces that promote efficient airflow. Hazardous gases and fumes are drawn down into a filtration system by the exhaust system as the welder operates, where they are cleaned and purified before being discharged back into the atmosphere. In order to improve use and convenience, several versions now come with integrated illumination, height adjustments, and tool storage choices.
Downdraft tables are very useful in industrial and workshop environments where several welding jobs are carried out concurrently. They lessen the chance of coming into contact with dangerous materials, lessen the need for extra ventilation systems, and improve visibility when welding. All things considered, downdraft weld tables are an excellent investment for enhancing workplace security, productivity, and adherence to health and safety standards in welding environments.
The Pros and Cons
Pros of Downdraft Weld Tables:
- Effective Fume Capture: Welders' air quality is improved by downdraft tables, which are made to suck smoke and fumes downward, successfully trapping dangerous airborne contaminants at the source.
- Enhanced Safety: These tables help create a safer workplace by lowering exposure to harmful particles and fumes, which lowers the health hazards related to welding activities.
- Integrated Workstation: Downdraft tables are practical and multipurpose workstations since they often include built-in features like integrated illumination, height adjustment, and tool storage.
- Reduced Need for Additional Ventilation: The integrated fume extraction system simplifies workspace design and may result in lower installation costs by reducing the need for separate ventilation systems.
- Versatility: Downdraft weld tables can be a useful addition to any workplace because they are appropriate for a wide range of welding jobs and materials.
Cons of Downdraft Weld Tables:
- Higher Initial Cost: Because of their sophisticated features and integrated fume extraction systems, downdraft tables can be more expensive than typical welding tables.
- Maintenance Requirements: To keep the table operating efficiently and extend its lifespan, regular maintenance is required. This includes cleaning the filters and making sure the exhaust system is operating correctly.
- Limited Size and Workspace: Downdraft tables may not be as appropriate for larger projects due to its design, which may restrict the size of the workpieces that can be handled.
- Noise Levels: In a busy workshop setting, the fume extraction system's operating loudness may necessitate the installation of additional soundproofing measures.
- Power Dependency: The fume extraction system of downdraft weld tables is dependent on electricity, which could cause problems in the event of a power outage or restricted access to electrical outlets.
Welding Tables:
Welding Booths with Ventilation Systems
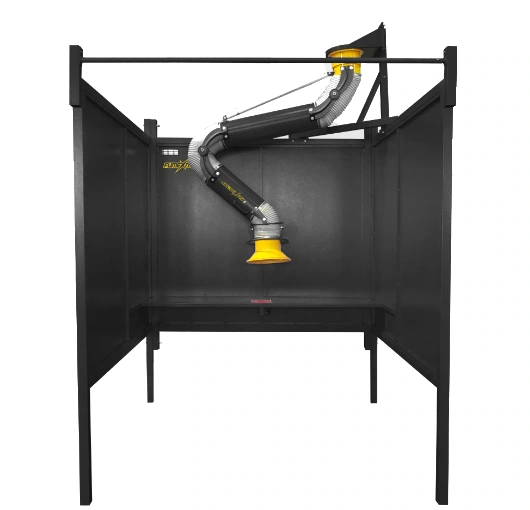
Specialized enclosures called welding booths with ventilation systems are made to ensure that welding operations take place in a controlled environment that complies with health and safety laws. In order to confine noise and pollutants produced during welding processes, these booths are built from sturdy materials and frequently include soundproofing elements. The ventilation system's main goal is to efficiently remove dangerous gases, fumes, and particulates created during welding so that welders may breathe cleaner air.
Welding booth ventilation systems are often installed overhead or on the side, drawing contaminated air through filters and then recirculating or expelling it outdoors. By doing this, the danger of respiratory problems for employees is decreased and the air quality is kept at its best. Ergonomic designs and adjustable lighting are other common features in welding booths, which improve comfort and visibility.
Welding booths are especially useful because they help control fumes and create a safer workplace when several welders are operating at once. They can also increase productivity by lessening airborne toxins and noise disturbances. All things considered, welding booths with ventilation systems are crucial purchases for businesses concerned with employee safety, legal compliance, and effective welding operations.
The Pros and Cons
Pros of Welding Booths with Ventilation Systems:
- Enhanced Worker Safety: Welders are considerably less likely to experience respiratory problems thanks to these booths' efficient absorption and filtering of dangerous gases, fumes, and particles.
- Controlled Environment: Welding booths offer a confined work area that reduces outside noise, distractions, and environmental influences, which enhances productivity.
- Compliance with Regulations: These booths, which come with ventilation systems, assist businesses in adhering to air quality requirements while also helping them to meet occupational health and safety standards.
- Noise Reduction: Soundproofing materials are frequently incorporated into the enclosed design of welding booths to assist lower noise levels and create a more comfortable working environment.
- Versatile Use: Welding booths are appropriate for a range of applications, from light to heavy-duty welding, because they can handle a variety of welding procedures and materials.
Cons of Welding Booths with Ventilation Systems:
- Higher Initial Investment: Initial budgets may be impacted by the high cost of buying and installing a welding booth with an integrated ventilation system.
- Space Requirements: These booths can take up a lot of room in a workshop, which could be an issue in settings that are more crowded or smaller.
- Maintenance Needs: To ensure peak performance, the ventilation system needs to be maintained on a regular basis, which raises the cost of continuous operations. Maintenance includes cleaning and filter replacement.
- Temperature Control Issues: In order to maintain a comfortable working temperature, enclosed booths may need to have additional climate control systems installed in case they get heated during operation.
- Potential Limitations on Mobility: Welders' freedom of movement may be restricted by welding booths' fixed design, particularly for larger jobs that need more room.
Welding Curtains with Ventilation Systems
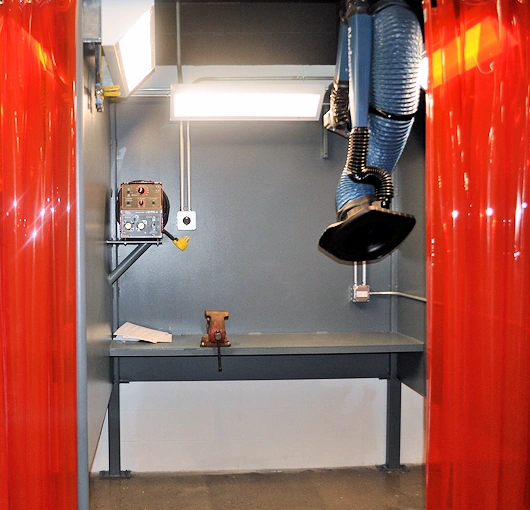
Essential safety equipment, welding curtains with ventilation systems are made to provide safe, regulated conditions for welding operations. The strong, fire-resistant materials used to make these curtains aid in containing heat, sparks, and dangerous ultraviolet (UV) light produced during welding operations. They shield other workers and equipment from potential dangers by enclosing the welding area.
These curtains, which incorporate ventilation systems, have elements that encourage airflow, making it possible to effectively remove the dangerous smoke and fumes produced during welding. Exhaust fans or ducting attached to the curtains can be used to provide ventilation, which will remove stale air from the workspace and replace it with clean air. This improves the quality of the air overall and lowers the possibility of respiratory problems for welders and other surrounding people.
Ventilation-equipped welding curtains are adaptable and simple to erect or take down, which makes them appropriate for both transient and permanent welding stations. They can help confine emissions and create a safer workstation, which makes them especially helpful in settings where many welding processes are taking place at the same time. All things considered, these goods are wise investments in terms of enhancing safety, adhering to health standards, and preserving a productive workplace for welding operations.
The Pros and Cons
Pros of Welding Curtains with Ventilation Systems:
- Improved Safety: Welding curtains improve overall workplace safety by efficiently containing sparks, spatter, and damaging UV radiation. This shields surrounding personnel and equipment from danger.
- Fume Control: By eliminating dangerous smoke and fumes created during welding, the integrated ventilation system helps to improve air quality and lower worker respiratory hazards.
- Flexible Setup: Welding curtains are ideal for both temporary and permanent welding stations in a variety of workspaces because they are simple to install, remove, or rearrange.
- Cost-Effective Solution: Welding curtains with ventilation systems are a less expensive way to provide safe welding conditions than building permanent walls or enclosures.
- Versatile Applications: These curtains can be utilized in a variety of locations, such as manufacturing facilities, building sites, and workshops, and they are appropriate for a range of welding operations.
Cons of Welding Curtains with Ventilation Systems:
- Limited Containment: Even though welding curtains offer some safety, their overall efficiency may be diminished because they may not be able to completely control fumes and sparks when compared to enclosed welding booths.
- Maintenance Needs: To guarantee optimum performance, the ventilation system needs to have regular maintenance, which can raise operating expenses. This maintenance includes cleaning and filter replacement.
- Potential for Wear: Welding curtains are susceptible to damage from heat, sparks, and chemicals over time, which can result in replacement and additional expenses.
- Space Requirements: Welding curtains may need enough room for efficient installation and airflow, depending on their size and arrangement. This might be an issue in busy areas.
- Noise Control Limitations: Welding curtains can reduce noise to some extent, but they don't give as much soundproofing as fully enclosed booths, which could expose workers to loud environments.
Respirators:
Respiratory Protective Equipment (RPE)

A vital part of occupational safety is respiratory protective equipment (RPE), which guards against breathing in dangerous airborne particles such dust, fumes, gasses, and vapors. RPE is available in several forms, each designed to meet the needs of a particular environment or set of dangers. Examples of these include masks, respirators, and air-purifying devices.
Air-supplied devices and filtering devices are the two primary categories of RPE. Filters are used by filtering devices—like reusable respirators or disposable masks—to collect airborne pollutants. They are categorized according to how well they filter, with some made to ward against particles and others against vapors and gases. Air-supplied devices, appropriate for high-risk workplaces or circumstances when the quality of the air is seriously deteriorated, supply clean, breathable air from an external source.
To guarantee that the equipment offers sufficient protection, appropriate selection, fit testing, and training are necessary for the effective use of RPE. To guarantee functionality, routine inspections and maintenance are also necessary. RPE is essential for safeguarding the health of employees, raising safety standards, and guaranteeing that occupational health laws are followed in a variety of sectors by lowering exposure to dangerous materials.
The Pros and Cons
Pros of Respiratory Protective Equipment (RPE):
- Health Protection: By removing dangerous airborne pollutants like dust, fumes, and poisonous gases, respirable particulate matter (RPE) considerably lowers the risk of respiratory illnesses and other health problems.
- Compliance with Regulations: By guaranteeing compliance with legal requirements and standards, the use of RPE helps enterprises comply with occupational health and safety legislation.
- Variety of Options: RPE is available in a variety of forms, such as powered air-purifying respirators, reusable respirators, and disposable masks, enabling customized solutions depending on particular settings and risks.
- Enhanced Worker Safety: RPE promotes a safer workplace by offering a dependable kind of protection, which raises employee morale and productivity since they feel confident in their safety.
- Cost-Effective Solutions: Numerous RPE alternatives, especially disposable masks, are simply deployed and reasonably priced, making them available to a broad range of businesses.
Cons of Respiratory Protective Equipment (RPE):
- Comfort Issues: Certain RPE, particularly full-face respirators, can be difficult to wear for extended periods of time, which lowers worker compliance.
- Proper Fit Required: A correct fit is necessary for effective protection. Safety may be compromised if RPE is improperly installed, allowing dangerous compounds to get through the filters.
- Maintenance Needs: To ensure effectiveness, reusable RPE needs to be cleaned, inspected, and maintained on a regular basis. This might take time and increase operating expenses.
- Limited Protection Duration: RPE filters may get saturated or clogged and need to be replaced often to keep them working properly, which could result in extra expenses.
- Potential for Over-Reliance: Employees who depend too much on protective equipment (RPE) may overlook alternative safety precautions and controls that could prevent exposure to risks in the first place.
Welding Exhaust Hoods:
Floor Mounted Welding Hoods - Strips
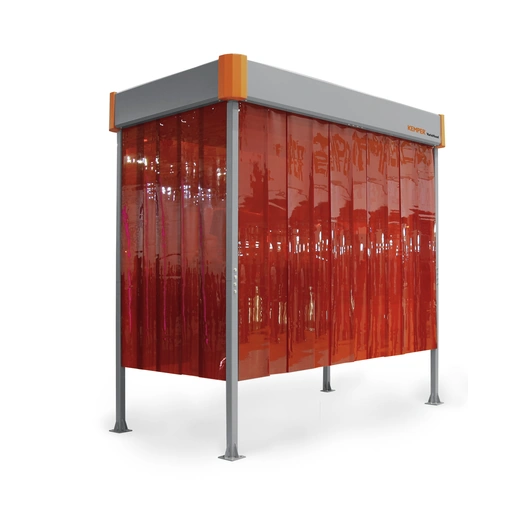
Specialized ventilation systems called floor-mounted welding hoods with strips are made to improve the quality of the air and increase safety in welding situations. These hoods, which are usually mounted at floor level, include a barrier surrounding the welding area made of a number of flexible or rigid strips. Their main job is to gather dangerous gasses, smoke, and fumes that are released during welding operations and send them into an exhaust system where they will be filtered and removed.
Because the strips assist trap and funnel impurities toward the hood, minimizing their dispersion into the surrounding workstation, floor-mounted hoods are designed to allow for effective ventilation. When numerous welders are operating simultaneously in high-output welding tasks, this design performs especially well.
These hoods frequently aid in shielding equipment and other workers from heat, sparks, and UV radiation released during welding in addition to extracting fumes. Numerous variants feature customizable features that enable placement flexibility according to particular welding tasks and configurations. In industrial and manufacturing environments, floor-mounted welding hoods with strips are crucial equipment for upholding a safe and regulated work environment, which enhances worker productivity and health.
The Pros and Cons
Pros of Portable Fume Extractors for Welding Fume Control:
- Mobility and Flexibility: Portable fume extractors are convenient for carrying to many welding locations and provide focused fume control wherever it's needed. This is particularly useful in large structures or places without designated welding assignments.
- Effective Fume Capture: When positioned close to the welding point, portable fume extractors efficiently capture emissions at the source, reducing airborne pollution in the workplace.
- Cost-Effective: Smaller companies or temporary setups might save money by using portable fume extraction systems, which are occasionally less expensive than permanent ones.
- Versatility: These extractors are a versatile instrument in a workshop or industrial setting since they may be used for various welding processes and other tasks that produce hazardous fumes.
- Easy Maintenance: Portable fume extractors are often designed to require little maintenance and come with easily interchangeable filters that can be cleaned or replaced as needed, ensuring continuous operation with little downtime.
Cons of Portable Fume Extractors for Welding Fume Control:
- Limited Coverage Area: Since portable fume extractors are designed to cover specific workstations, larger spaces or several welding stations may require more than one unit if mobility is a concern.
- Dependence on Proper Positioning: The main factor affecting a portable fume extractor's efficiency is how close it is to the welding source. Inappropriate placement may reduce its efficiency, which raises the pollution level in the air.
- Noise Levels: Some portable fume extractors have loud operating noises, which may annoy workers or be distracting in a busy office.
- Frequent Filter Replacement: Depending on how much they are used, portable fume extractor filters may need to be changed or cleaned frequently. This could result in ongoing maintenance costs and possible downtime.
- Power Requirements: Due to their necessity for a power supply, portable fume extractors may not be able to be used in some locations and may require additional extension cords or power outlets, which could lead to a cluttered workspace.
Hanging Welding Hoods - Strips
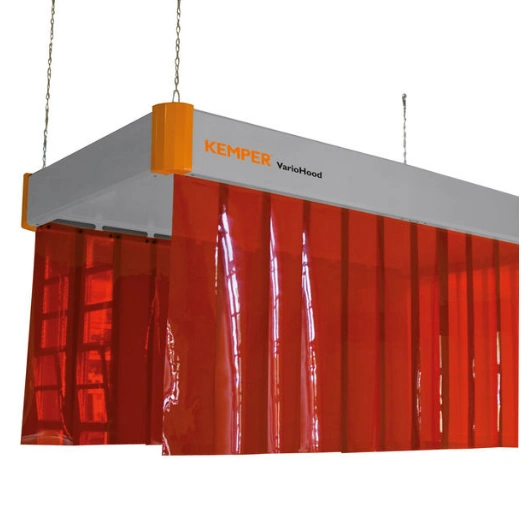
Innovative ventilation solutions like hanging welding hoods with strips are made to enhance safety and air quality in welding situations. These hoods, which are suspended from ceilings or overhead structures, have flexible or rigid strips that enclose the welding area and capture dangerous gases, smoke, and fumes generated during the welding process. Because of their raised design, which promotes effective airflow, pollutants are drawn upward and sent into an exhaust system where they are filtered and removed.
In addition to containing welding byproducts, the strips also reduce the risk of sparks and UV radiation spreading, safeguarding nearby personnel and equipment. Because they efficiently control airborne pollutants, hanging welding hoods are especially useful in settings where numerous welding processes take place at the same time.
Because many hanging hoods are movable, users can arrange them to suit particular welding jobs and configurations. By lowering exposure to dangerous compounds and enhancing general air quality, they can also improve worker comfort. These hoods also assist companies in adhering to occupational health and safety laws, which promotes a safer workplace. All things considered, hanging welding hoods with strips are crucial equipment for upholding safety regulations and fostering efficiency in manufacturing and industrial environments.
The Pros and Cons
Pros of Hanging Welding Hoods - Strips:
- Efficient Fume Extraction: By efficiently capturing smoke and dangerous gases at their source, hanging hoods improve workplace air quality and lower employee health hazards.
- Space-Saving Design: These ceiling-mounted hoods are perfect for congested workshops or spaces with limited equipment space since they save important floor space.
- Flexible Configuration: Many hanging hoods are movable, which increases their adaptability by letting them be positioned according to certain welding jobs and workplace requirements.
- Protection from Sparks and UV Radiation: The strips contribute to the containment of sparks and UV emissions, adding an extra degree of safety for workers in the vicinity and shielding equipment from harm.
- Compliance with Safety Regulations: By installing hanging welding hoods, businesses can ensure that welding operations take place in a safer environment and comply with occupational health and safety standards.
Cons of Hanging Welding Hoods - Strips:
- Initial Installation Costs: The initial expenses associated with buying and installing hanging hoods might be high, particularly if more infrastructure is required for support.
- Maintenance Requirements: To guarantee peak performance and air quality, regular maintenance is required, which includes cleaning and inspecting the exhaust systems and hoods.
- Limited Mobility for Workers: Welders may find it difficult to maneuver around fixed hanging hoods, especially on larger projects where there may be more flexibility in equipment usage or arrangement.
- Potential for Noise: Noise from the ventilation system's functioning may require extra precautions to control noise levels in crowded work areas.
- Height Limitations: There might be restrictions on how low the hoods can hang depending on the height of the ceiling, which could affect their usefulness and usability in particular situations.
Hanging Welding Hoods - Large
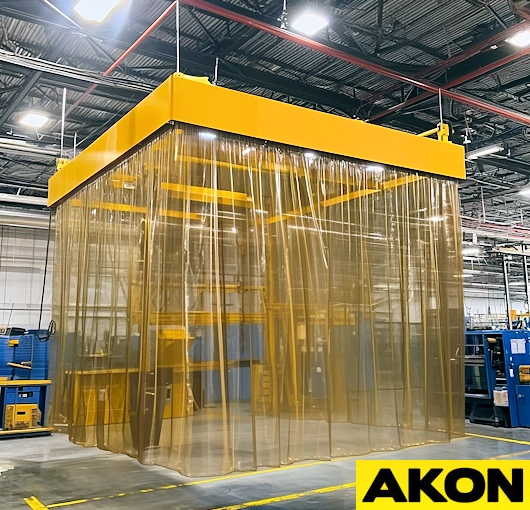
Larger models of hanging welding hoods are specialist ventilation systems made to improve safety and air quality in welding locations where heavy operations take place. These enormous hoods, which are suspended from ceilings or above frames, are designed especially to collect and filter dangerous gases, smoke, and fumes released during welding operations. They efficiently route airborne contaminants into an exhaust system for adequate filtration and disposal, making them suitable for facilities with several welding stations or high-output processes. Their vast covering area further enhances their appeal.
Large hanging hoods are designed to provide the best possible airflow, which ensures that pollutants are efficiently collected before they spread across the surrounding area. This containment helps shield other workers and equipment from heat, sparks, and ultraviolet (UV) radiation released during welding operations in addition to improving the general quality of the air.
Large hanging hoods are often adjustable, allowing users to place them in accordance with particular welding jobs and configurations. They are essential to keeping the workplace safe and in compliance with OSHA and other safety and health laws. Large hanging welding hoods are crucial equipment for supporting worker health, raising output, and creating a secure work environment in factories and fabrication plants.
The Pros and Cons
Pros of Hanging Welding Hoods - Large:
- Extensive Coverage: Large hanging hoods are perfect for facilities with numerous welding stations or intensive welding operations because they offer a wider area of fume extraction.
- Efficient Air Quality Improvement: The overall air quality in the workspace is greatly improved by these hoods since they efficiently trap dangerous gases, smoke, and odors right at their source.
- Space-Saving Design: Large hanging hoods free up important floor space by hanging from the ceiling, which improves organization and mobility in the workshop.
- Protection from Hazards: By reducing heat, UV rays, and sparks, the design protects surrounding personnel and equipment from welding-related risks.
- Compliance with Safety Standards: Large hanging hood installation promotes a safer workplace by helping businesses comply with occupational health and safety laws.
Cons of Hanging Welding Hoods - Large:
- High Initial Costs: Large hanging hood installation and acquisition might be expensive up front, especially for companies with limited resources.
- Complex Installation: Specialized support structures and labor may be needed for installation, which would increase the setup costs and duration.
- Maintenance Requirements: To guarantee optimal performance, routine maintenance is required, which can raise operating expenses. This maintenance includes cleaning and filter replacement.
- Fixed Positioning: Even though they are movable, big hanging hoods can nevertheless restrict an employee's range of motion, particularly in busy workplaces where shifting positions regularly occurs.
- Potential Noise Levels: Noise from the ventilation system's functioning may require extra precautions to control noise levels in crowded workshops.
Welding Area Contaiment:
Capturing welding smoke in a defined area (welding zone) of your facility is a great final step to ensure workers who are not welding are not exposed to welding smoke haze. Welding fume vacuums are great for capturing the majority of welding fumes, but they do not capture 100% of the fumes. Enclosing the area with large curtain walls fixes this issue when used in conjunction with heating, ventilation, and air conditioning (HVAC) and variable-frequency drives (VFDs). Below you will find more information on welding curtain wall ideas to enclose your welding areas.
Its important to note that the enclosure should go from floor to roof deck or be freestanding with a ceiling to make a welding enclosure. The enclosure must work in conjunction with an air filtration device to exhaust the welding fumes as to not harm the people inside of the area.
Welding Fume Enclosures - Large Area - Style 1
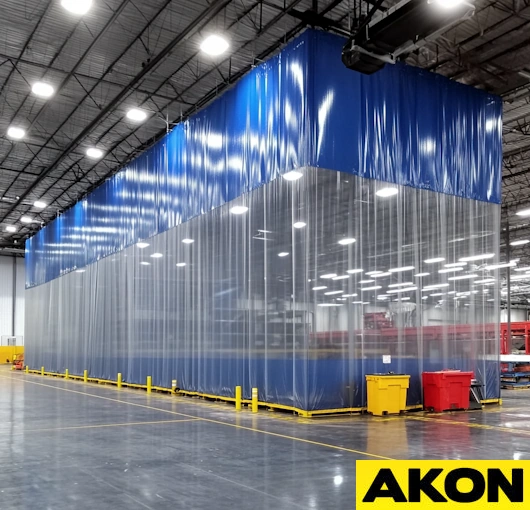
An efficient way to restrict welding fumes inside designated areas and stop them from permeating a whole facility is using vinyl curtain walls running floor to ceiling. Durable, fire-resistant vinyl material makes these curtains able to survive the intense heat and sparks connected with welding operations. These curtain walls help to separate welding fumes by building a physical barrier, therefore ensuring their confinement to the intended welding region. Maintaining air quality throughout the remainder of the plant depends on this, which also shields workers from harmful pollutants.
Apart from fume control, vinyl curtain walls provide simplicity of installation and versatility. Usually mounted on rails, they may be readily retracted or relocated as necessary and are custom-sized to meet any workstation. Their versatility makes them perfect for dynamic offices where the layout might be changed often. Moreover, by reducing the spread of airborne pollutants and so enhancing general worker safety, these curtain walls enable facilities to follow safety rules.
In welding and industrial environments, floor-to-ceiling vinyl curtain walls are generally a sensible and effective way to improve air quality and guarantee a safe working environment.
The Pros and Cons
Here are five pros and cons of using vinyl curtain walls that extend from floor to ceiling for containing welding fumes:
Pros:
- Effective Fume Containment: Vinyl curtain walls physically confine welding fumes to the designated area, preventing them from spreading throughout the building and enhancing overall air quality.
- Flexibility: These incredibly adaptable curtains can be adjusted to fit various workplace sizes. They are appropriate for dynamic work environments due to their ease of retraction, movement, and reconfiguration.
- Cost-Effective: Vinyl curtain walls offer a more cost-effective solution for fume containment than erecting permanent walls or expensive ventilation systems, especially for small to medium-sized enterprises.
- Ease of Installation: Quickly install vinyl curtain walls with minimal disruption to the existing workstation. They can be placed on tracks or rollers for quick deployment.
- Fire Resistance: Many vinyl curtain walls, which are composed of fire-resistant materials, provide additional safety by reducing the likelihood that a fire will spread in the event that sparks or intense heat from welding occur.
Cons:
- Durability Issues: Despite its durability, vinyl curtains can sustain wear and tear over time, especially in high-traffic areas or locations where they are frequently moved. They may require replacement or regular maintenance.
- Limited Insulation: There is hardly much thermal or acoustic insulation value in vinyl curtain walls. It may not be possible for them to manage the temperature or muffle noise in other parts of the building.
- Aesthetic Impact: When compared to more permanent choices, vinyl curtain walls may not be as aesthetically pleasing to some facilities, which could have an impact on how the workspace looks overall.
- Not a Complete Solution: Vinyl curtain walls are excellent for containment, but they might not be able to totally exclude welding fumes on their own. Safety requirements can still necessitate additional air filtration or ventilation equipment.
- Potential for Gaps: The capacity of the curtains to regulate odors may be compromised by improper installation or maintenance, which could leave gaps between the curtains and the floor or ceiling and perhaps allow pollutants to escape.
Welding Fume Enclosures - Large Area - Style 2
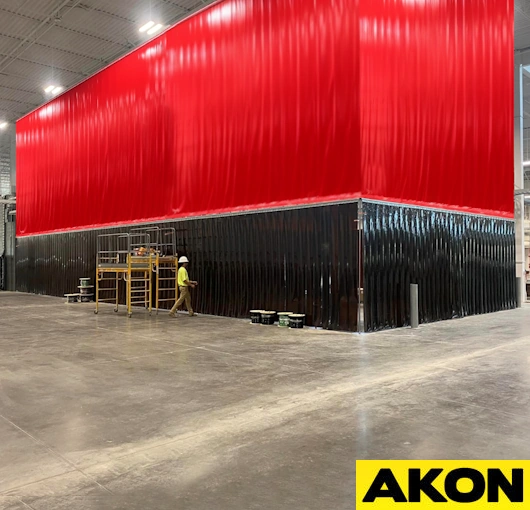
Using an enclosure with vinyl strip curtains on all four sides will effectively restrict welding fumes inside specified regions while also providing simple access for persons and material. Without rolling-up or swinging doors, these enclosures' 8-foot high strip curtains at the bottom help mobility in and out of the area. Freestanding hardware supports the strips, creating a flexible and easily available entrance.
Using aluminum angle brackets, top valance curtains constructed from sturdy, fire-resistant vinyl material are raised above the strip curtains onto the roof deck. This configuration guarantees that the enclosure stays strong and efficient in resisting the strong heat and sparks connected with welding activities. The vinyl curtains physically separate welding fumes to the targeted area, therefore preserving air quality throughout the remainder of the facility and shielding employees from dangerous contaminants.
Apart from fume control, this enclosure system provides simplicity of installation and flexibility. The changeable access made possible by the strip curtains makes them perfect for settings where the arrangement might be changed regularly. These enclosures improve general worker safety by stopping the spread of airborne pollutants, therefore enabling facilities to comply with safety standards. This makes them a sensible and efficient solution for guaranteeing a safe working environment in welding and industrial environments and so enhancing air quality.
The Pros and Cons
Pros of Welding Fume Enclosures:
- Effective Containment: By capturing and containing dangerous gases, smoke, and particulate matter at their source, welding fume enclosures greatly enhance the quality of the air in the workspace.
- Enhanced Worker Safety: These enclosures protect workers' health by limiting their exposure to harmful welding fumes, which lowers their risk of respiratory disorders and other health concerns.
- Flexible Configurations: Numerous enclosures are adaptable and customizable to suit different welding configurations, accommodating a range of welding tools and processes.
- Noise Reduction: Welding fume enclosures can aid in lowering welding operation noise levels, making the workplace calmer and improving worker comfort levels all around.
- Compliance with Regulations: Employing welding fume enclosures helps businesses comply with air quality and worker safety rules while also helping them satisfy occupational health and safety standards.
Cons of Welding Fume Enclosures:
- High Initial Costs: Welding fume enclosures can be expensive to buy and install, which could be a deterrent for smaller companies or those with tighter resources.
- Space Requirements: Fume enclosures can occupy a significant amount of floor space, depending on their size and design. This could be a problem in busy manufacturing or workshop spaces.
- Limited Mobility: Welding fume enclosures can restrict personnel and equipment movement once they are installed, making it difficult to adjust to new activities or processes.
- Maintenance Needs: To guarantee the enclosure operates at its best, regular cleaning and maintenance are required. This includes inspecting the enclosure and replacing the filters, which can raise operating expenses.
- Potential for Over-Reliance: Employees may grow reliant on fume enclosures for protection, possibly ignoring other crucial safety precautions and controls that lower exposure to dangerous materials.
Welding Fume Enclosures - Small Area - Style 1
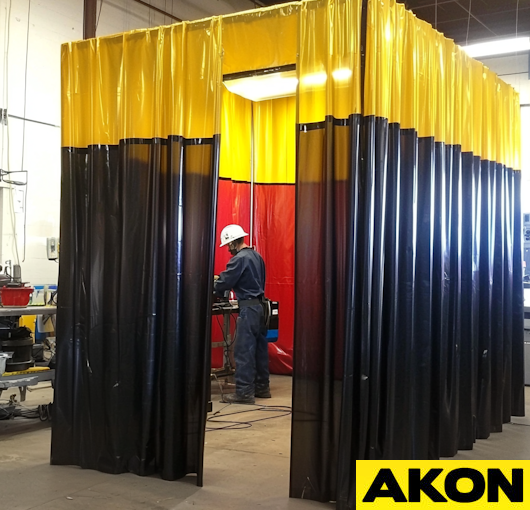
Compact ventilation systems known as small welding fume enclosures are made expressly to collect and filter dangerous smoke, fumes, and particulates produced during welding operations in constrained areas. These enclosures provide a concentrated area for efficient fume extraction, making them perfect for workshops or other spaces where floor space is at a premium.
Small welding fume enclosures are often made of sturdy materials and have built-in filtering systems that pull in contaminated air and filter out dangerous contaminants, creating a safer and cleaner work environment. Their small size makes them adaptable, making it simple to incorporate them into different welding configurations, whether in a separate welding booth or next to other pieces of equipment.
Light-duty welding applications, such small-scale fabrication or maintenance chores, are especially well-suited for compact enclosures. By drastically lowering exposure to harmful gases and enhancing general air quality, they offer vital safety for welders and other adjacent workers.
Many variants are portable and adjustable, allowing users to move them about as needed for various tasks. All things considered, compact welding fume enclosures are a useful way to improve safety and adherence in cramped spaces while guaranteeing that employees can work efficiently and comfortably.
The Pros and Cons
Pros of Small Welding Fume Enclosures:
- Space Efficiency: Because they can fit into small places, small welding fume enclosures are perfect for workshops that don't have enough room for larger equipment.
- Effective Fume Capture: By efficiently containing and filtering smoke and hazardous gases at their source, these enclosures greatly enhance worker safety and air quality.
- Portability: Numerous compact fume enclosures are lightweight and portable, making it simple to move them in accordance with particular welding activities or requirements.
- Cost-Effective: For facilities that need fume management without making a big investment, tiny enclosures are a cost-effective solution because they are typically less expensive than bigger fume extraction systems.
- Easy Integration: Because of their small size, they can be easily incorporated into current workflows and accommodate different welding settings without needing significant changes to the workplace.
Cons of Small Welding Fume Enclosures:
- Limited Coverage Area: When several welders are operating simultaneously in larger or high-output welding processes, the smaller size may limit the efficacy of fume capture.
- Lower Filtration Capacity: Compared to bigger systems, smaller enclosures could have less airflow and filtering capacity, which could mean more frequent filter replacements.
- Potential for Over-Reliance: Employees may disregard other crucial safety precautions and controls in favor of relying only on tiny enclosures for fume extraction.
- Maintenance Requirements: Maintaining optimal performance requires routine maintenance, which can add to the workload. This maintenance includes cleaning and filter changes.
- Noise Levels: Small fume enclosure operation can produce noise, which, if not adequately controlled, could make the workplace less comfortable.
Welding Fume Enclosures - Small Area - Style 2
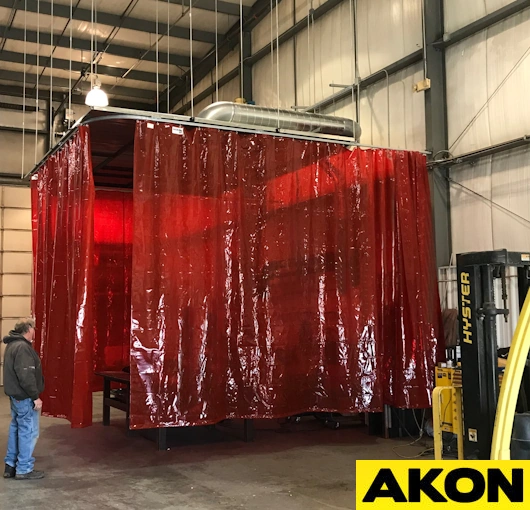
An efficient way to restrict welding fumes inside designated areas and stop them from permeating a whole facility is using vinyl curtain walls running floor to ceiling. Durable, fire-resistant vinyl material makes these curtains able to survive the intense heat and sparks connected with welding operations. These curtain walls help to separate welding fumes by building a physical barrier, therefore ensuring their confinement to the intended welding region. Maintaining air quality throughout the remainder of the plant depends on this, which also shields workers from harmful pollutants.
Apart from fume control, vinyl curtain walls provide simplicity of installation and versatility. Usually mounted on rails, they may be readily retracted or relocated as necessary and are custom-sized to meet any workstation. Their versatility makes them perfect for dynamic offices where the layout might be changed often. Moreover, by reducing the spread of airborne pollutants and so enhancing general worker safety, these curtain walls enable facilities to follow safety rules.
Hanging welding curtains can be used to isolate individual or multiple welding booths, or simply as a single dividing welding wall. AKON can take your design and make the hanging welding curtains into almost any configuration, depending on what you need. When your curtains are hung from above, retracting them grants you a completely open space. They also have the ability to roll around the corner, utilizing radius corners.
The Pros and Cons
Welding Fume Enclosures - Small Area - Style 3
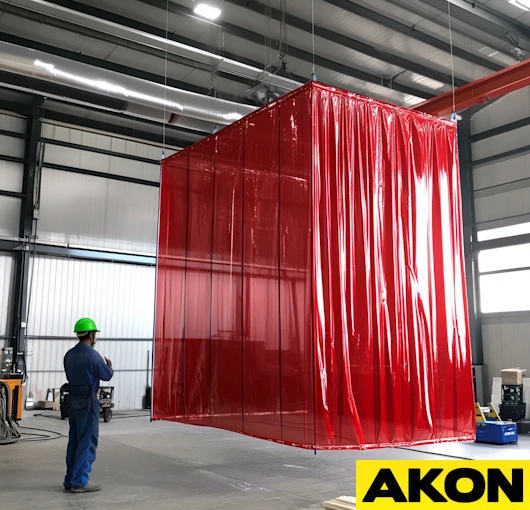
Roof from ceiling supports with static curtain and portable fume extraction. Static curtains and portable fume extractor systems mounted on roofs from ceiling supports are practical ways to improve air quality and safety in a range of manufacturing and industrial settings. Static curtains, which act as barriers to confine fumes, smoke, and airborne particulates produced during procedures like welding, grinding, or chemical handling, are suspended from ceiling supports, which offer a strong foundation. Usually constructed of sturdy, flexible materials, these curtains are impervious to adverse weather and capable of efficiently trapping pollutants.
Portable fume extraction devices can be used anywhere in the workspace and are frequently positioned on wheels or have handles. Strong fans and filtration technology in these systems trap dangerous gases at their source, keeping them from spreading into the surrounding region. Static curtains and portable extraction units work together to produce a controlled environment that enhances air quality and shields employees from potentially harmful exposure.
This arrangement improves both operational efficiency and safety since it frees workers from the distraction of toxic vapors as they work on their responsibilities. Furthermore, because of their adaptability to various work processes and shifting facility needs, portable extraction systems guarantee efficient fume management at all times.
The Pros and Cons
Pros of Roof from Ceiling Supports with Static Curtains and Portable Fume Extraction:
- Effective Containment: By keeping vapors and particles contained within a predetermined zone, static curtains reduce worker exposure and enhance the general quality of the air in the workplace.
- Flexibility and Mobility: The facility can readily adjust to changing processes and jobs by moving portable fume extraction units to different places as needed.
- Cost-Effective Solution: Smaller companies may find it more cost-effective to combine ceiling supports, static curtains, and portable extraction systems than to construct permanent fume extraction systems.
- Improved Safety: This configuration improves worker safety and lowers the risk of respiratory disorders and other health issues related to airborne pollutants by capturing dangerous gasses at the source.
- Easy Installation: Static curtains on ceiling supports are a practical solution for many businesses because they are reasonably simple to install and require little alteration to existing facilities.
Cons of Roof from Ceiling Supports with Static Curtains and Portable Fume Extraction:
- Limited Coverage Area: Static curtains are less appropriate for bigger workspaces or high-output processes with several workstations since their usefulness may be limited to smaller zones.
- Maintenance Requirements: To maintain peak performance and air quality, portable extraction devices require routine maintenance, which includes cleaning static curtains and replacing filters.
- Noise Levels: If portable fume extraction systems are not correctly handled, the noise they produce during operation may make the workplace less comfortable.
- Potential Instability: Safety risks could arise in the workplace if ceiling supports or portable components are not fitted properly and end up toppling over or getting dislodged.
- Reliance on Manual Operation: Compared to fixed extraction systems, portable systems would need more frequent human operation and monitoring, which could be less practical in hectic work conditions.
Common Questions
What is ambient air filtration?
Ambient air filtration is the process of cleaning the air over a whole facility therefore removing environmental pollutants. Whereas source capture systems trap pollutants exactly at their source, ambient systems are meant to move and filter the air all about a room or building. They so operate like ordinary exhaust ventilation systems but they incorporate filters to remove pollutants. Either the filtered air can be recirculated back into the facility or vents outdoors.
Which welding techniques cause the most fumes?
Compared to resistance welding or laser welding, consumable welding—including MIG (GMAW), TIG (GTAW), arc welding, stick welding, and flux-cored welding—tends to produce more fumes. Most of the weld fumes come from the consumables these operations utilize. But especially when working with coated or galvanized metals, resistance and laser welding can potentially create dangerous vapors. See the following materials to better grasp the health hazards related to different welding techniques:
Do systems for ambient fume capture call for ducting?
System of ambient fume capture can be either ducted or ductless. Under a ducted system—that is, a conventional push-pull arrangement—a network of ducts pulls in contaminated air from one side and releases clean air from the other. normally constructed close to the ceiling to capture pollutants as they rise, these ducts are linked to a sizable dust collector normally found outside the building.
By contrast, ductless ambient fume collection systems depend on several smaller dust collectors placed all about the building. These devices generate airflow patterns that move contaminated air away from employees and re-circulate clean air into the room. Often fitted with movable louvers to properly direct airflow, the ductless collectors contain intake and exhaust plenums.
Summary
As shown above, there are several approaches to effectively managing weld fume in big-part welding. Every solution comes with compromises on worker protection, cost, and performance. Your solution really has a direct relation to the size of your welding operation. For instance, a shop with 1-2 welders will not need the same configuration as a manufacturing facility with 50-100 welders. With that, this chart will help you determine which solution is best for you.
You can see that for both small scale and large scale welding operations there should be a localized fume extraction device used in conjunction with a containment area device such as a welding curtain, hard wall, panel wall, etc. One device used alone is not an a sufficient solution to protect both the welder(s) and the non-welder(s) in the area. The ideal setup for both big and small welding operations is to use local welding fume capture devices in conjunction with a general area containment solution.
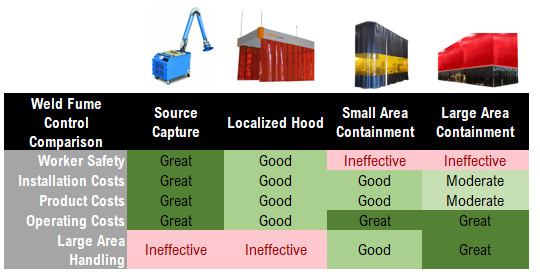