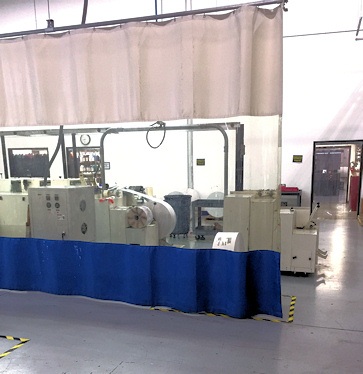
Introduction
One challenge every business face is the maximizing of space available to them. This is as a result of either to cope with an increase in business or to accommodate a new production line of the business. Therefore businesses demand an effective solutions to provide them with the required chunk of space needed for that increase in their facility.
Before now, business has been plunged to know just one solution for space maximization, which is a conventional extension and expansion development. However, we will be reviewing the disadvantages of extension and introducing a cost-effective solution from AKON. This alternative solution will overcome challenges related to traditional partitioning methods.
The Problem With Production Line Expansions
Permanence
Change is constant and every business that grows needs to adapt in terms of the business. Using the traditional expansion as a solution for maximizing space is sometimes a problem when there is a new production line and there is need to adjust the facility to accommodate this new production.
Time
Time they say is money. The conventional extension takes time to prepare especially when the size and scale of the expansion are huge. Building this extension will take a couple of months, which is not good for the business if time is considered and space is needed on time.
Expensive
A conventional expansion is expensive to build and when it takes time to get ready, it demands more finance. If the budget for expansion is low and has to be strictly adhered to then the traditional expansion is the wrong solution for maximizing space in any business facility.
Extensive Ground-works
Conventional extension demands ground-work which is generally disorderly to the existing process, this, in turn, will increase the time needed to complete the extension which will demand more finance. The conventional extension is a permanent feature that cannot adapt easily should the needs of the business change
Production Line Partitions for Maximising Space
Now let us introduce you to a new solution that is not just cost-effective but can adjust to your new production line in your facility.
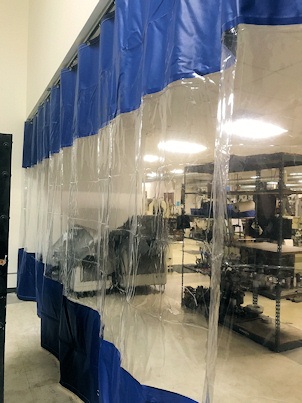
Installation
The installation process is fast and takes less time to start running, unlike a typical rigid wall extension which consumes time and finance. The installation of a new production curtain and divider has little or no effect on other processes as they can work efficiently as a new curtain and divider is installed. The installation of a this device normally takes hours or sometimes a few days depending on the size and number of curtains needed in the facility. Compare this to the weeks and months of building a conventional rigid wall extension.
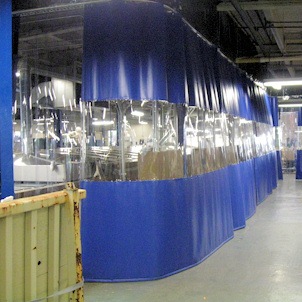
Cost-effective
AKON makes use of reinforced PVC material in manufacturing the production curtain and dividers, making it cost-effective and adaptive to a new process. It is unmatched with the traditional partitioning methods which are far more expensive to build.
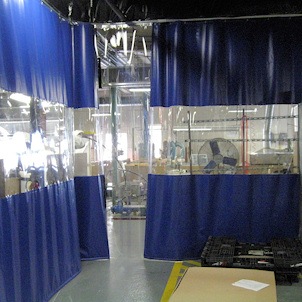
Minimal Floor Space
Unlike the traditional curtain partitions, the curtains demand less floor space to support the structure, thereby increasing floor space and maximizing space. AKON production expansion curtains are lightweight and suspended from the ceiling. They can also be free-standing on pedestals if there are overhead obstructions. When used as assembly line curtains they can feature strip door entrances to allow for rapid access.
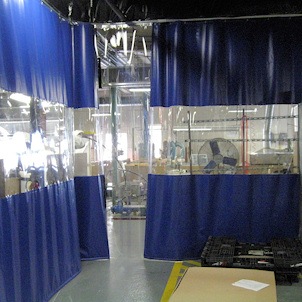
Minimal Floor Space
Unlike the traditional curtain partitions, the curtains demand less floor space to support the structure, thereby increasing floor space and maximizing space. AKON production expansion curtains are lightweight and suspended from the ceiling. They can also be free-standing on pedestals if there are overhead obstructions. When used as assembly line curtains they can feature strip door entrances to allow for rapid access.
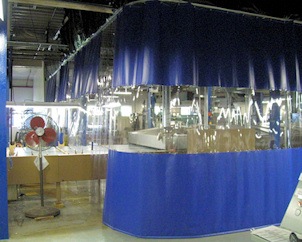
Permanent and Portable
One of the major benefits of a factory production curtain is that whilst they are permanent, they can also be moved or relocated to a new process and will adapt without causing any contamination. Its portability makes it flexible for business should the need of business change further, they can adapt to the new developments without major disturbance to manufacturing processes.
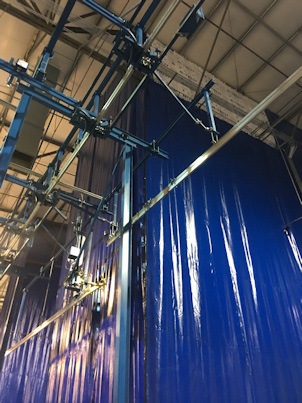
Special Purpose
Specific sectors require certain industrial curtain partitioning that can be produced to suit certain situations. Materials used for such sectors should have various properties that should be beneficial and will not cause contamination in sectors such as anti-fungal, food safety, flame resistant thermal and anti-static etc.
Any Layout For Your Needs
Curtain Track
- 16 gauge galvanized steel tracks
- Nylon roller hooks for easy opening
- 6 mounting styles to connect to various structures
- Free standing hardware for up to 20' in height
Static Mount Hardware
- Aluminum Angle - Use with self tapping Tek screws to pinch curtain to angle.
- Grommets Only - You can then use many DIY methods to hang the curtains.
- Beam Clamps - Clamps onto the flange of beams, joists and purlins.